About
About Us
Pure Piping delivers reliable, high-quality piping systems, fabrication and installation services to the pharmaceutical, cosmetic, semiconductor and bioprocess industries. The company directors have a combined over 50 years of experience in fabrication, project management and supervision in the industry. They intimately understand the environments in which we work and help clients get it right the first time. The result is exceptional quality.
The Pure Piping team rigorously applies the company Quality, Administrative and Technical Operations Management system in its day-to-day activities, allowing for the execution of projects in a standard and systemised manner.
We have completed several large-scale projects over the past eight years.
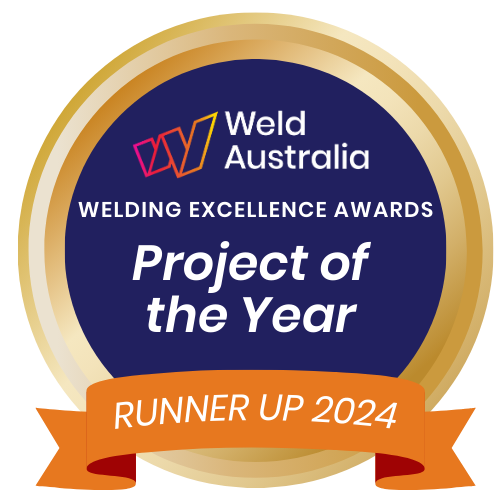
Quality Assurance
Pure Piping strives to produce the highest Quality Assurance documentation possible. The QA pack we provide for our clients is set out in an obvious, practical way that captures all required components of the project. We ensure our documentation meets or surpasses the required standards as per our clients’ regulating bodies such as the Therapeutic Goods of Australia (TGA) or the Australian Pesticides and Veterinary Medicines Authority (APVMA).
Our quality pack complies with all codes of GMP (Good Manufacturing Practice), is equivalent to ISO 9001 and is prepared following AS/NZS ISO 9004.5
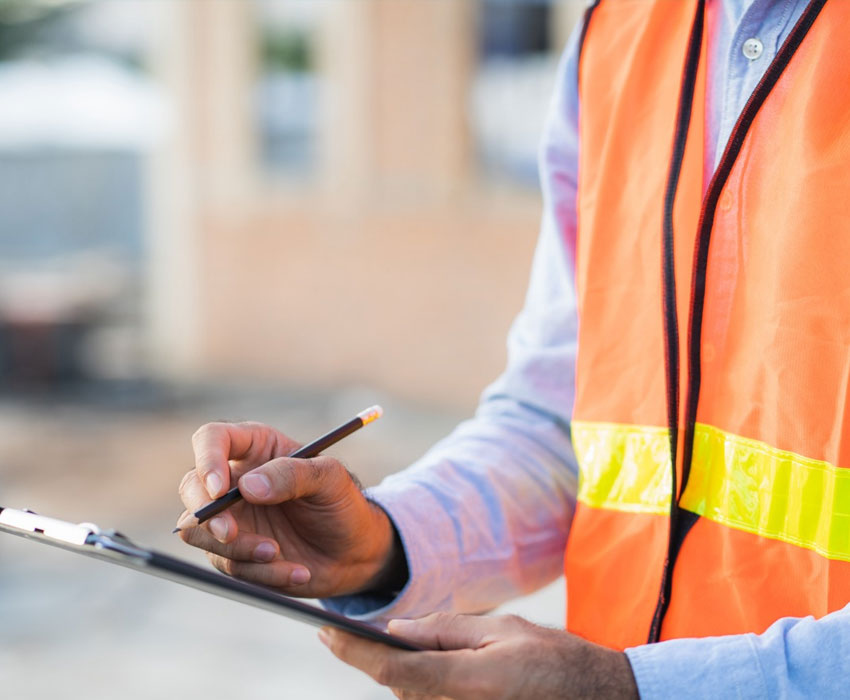
Our Premises and equipment
We have a custom-fitted 700m2 factory at 32 The Concord, Bundoora.
Our factory is home to equipment such as our forklift, brake press, band saws, pedestal drill, polishing grinders and a range of material stock.
To ensure a superior finished product Pure Piping uses high-quality, well-maintained welding equipment both in our factory and onsite.
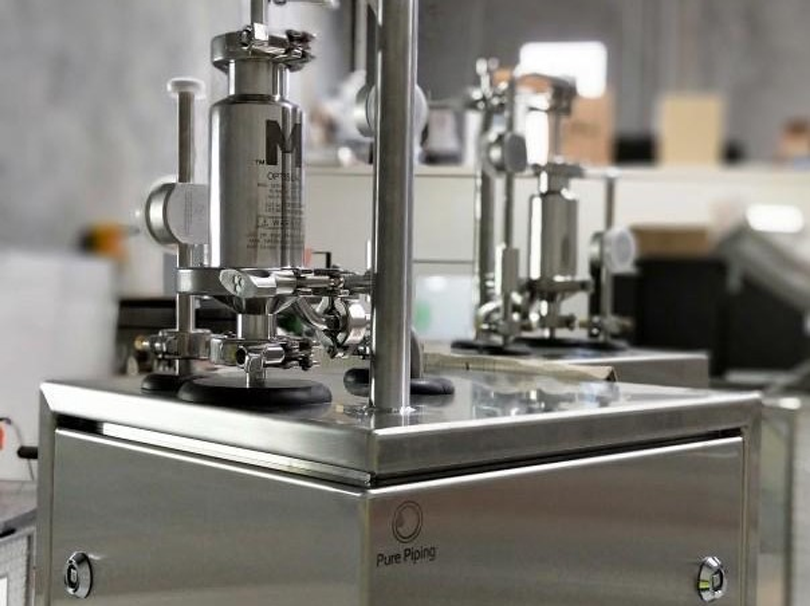
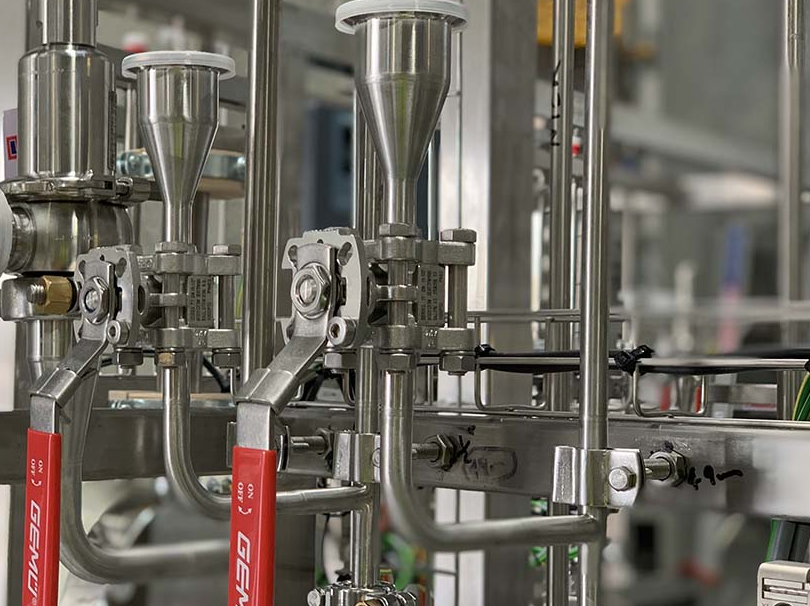
- 12x OrbimatOrbital Welding Machines, all with test and calibration certificates.
- 1x Orbitwin 165CA Parallel Switching Box which allows for the connection of two welder heads from one machine.
- 1x OW12 weld head, weld range3-12mm.
- 3x OW17weld head, weld range 6mm-13mm.
- 3x 38S weld heads, weld range 6mm-38mm.
- 8x 76Sweld heads, weld range 6mm-76mm.
- 2x 115S weld head, weld range 25mm-115mm.
- 1x 170S weld head, weld range 25mm-170mm.
- 36x TIGwelding machines.
- 12x specialist tube cutting machines.
- 7x tube end facing tools, ensures perfect square tube ends for precision orbital welding.
- Magnehelic–With our extensive experience welding small size pipe/tube, we know how to ensure correct internal gas pressure using a Magnehelic.
- Purge Monitor–Our calibrated gas monitors enable us to know for certain all oxygen is removed from the line during purging, ensuring we provide the cleanest internal welds possible.
- 12x Laser levels–Our calibrated laser levels ensure our pipework and equipment is installed accurately to the project specifications.
- 2x Passivation Skids–Manufactured in house to ensure all requirements could be catered for. Skid options-800L tank for large applications, 80Ltank for smaller applications
- 1x Agilent Helium Leak Detector
- 1x BeckmanCoulter Particle Counter
- 2x TPS WP-81 Conductivity, pH and Temperature Meters
Our Team
Pure Piping trade personnel are second-to-none in the field, highly qualified, experienced and committed to working alongside our clients to provide exceptional results.
Pure Piping employees are all entitled to the PPTEU’s enterprise bargaining agreement (EBA).
The decision for our company to sign the EBA was to ensure our employees work under the best industry agreement and entitlements for them (e.g. RDOs, holiday leave, long service leave, redundancy fund).
The best conditions ensure we have the best employees in our unique high-purity industry.

Food, Beverage and Pharmaceutical
ASSDA FABRICATOR PROJECT OF THE YEAR 2022
Pure Piping
Project:
CSIRO GMP Facility
www.purepiping.com.au
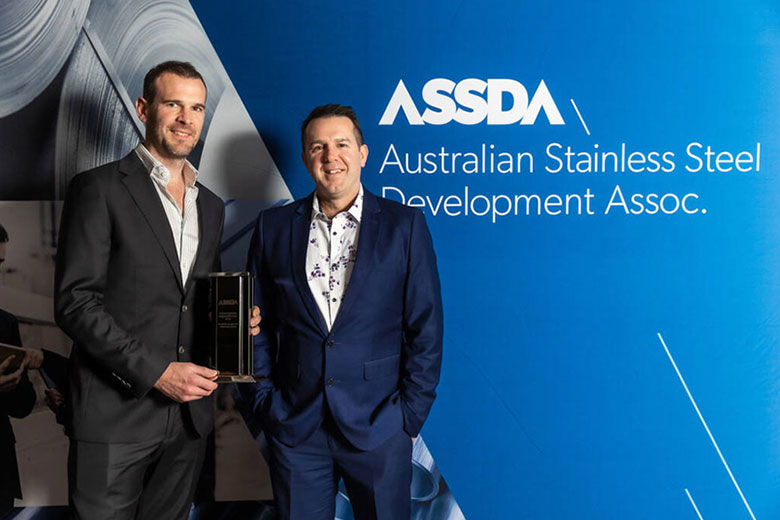
Food, Beverage and Pharmaceutical
ASSDA FABRICATOR PROJECT OF THE YEAR 2023
Pure Piping
Project:
Project Hawara, CSL Global Headquarters
www.purepiping.com.au
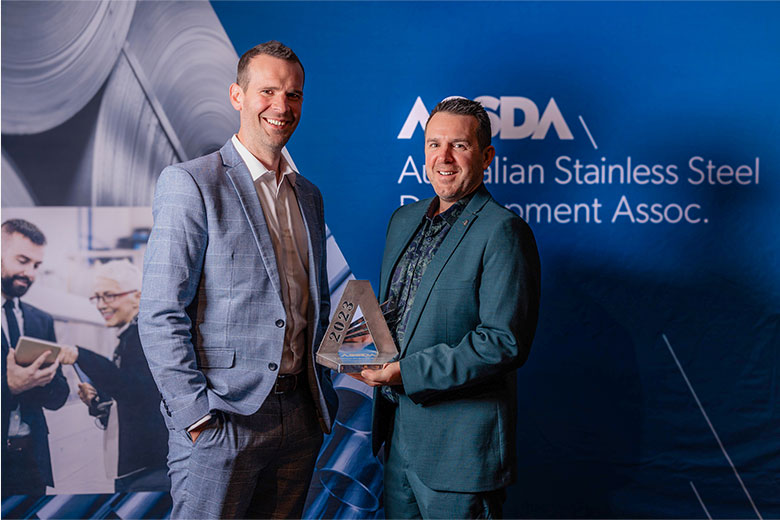
Our Team
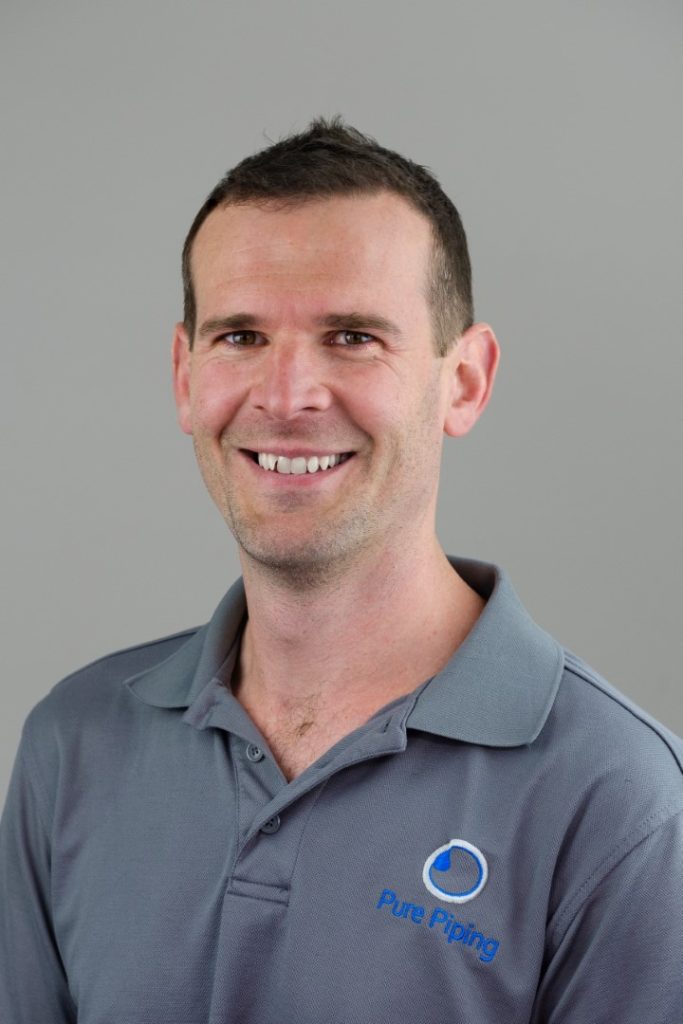
Andrew Owen
Founder - Director
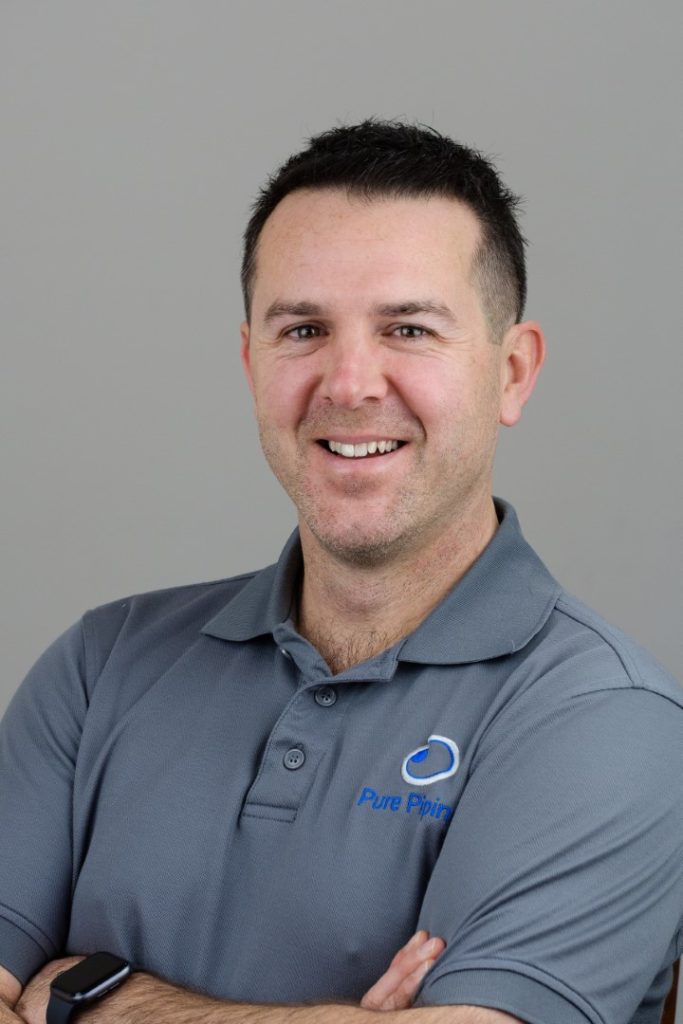
Mark Owen
Director
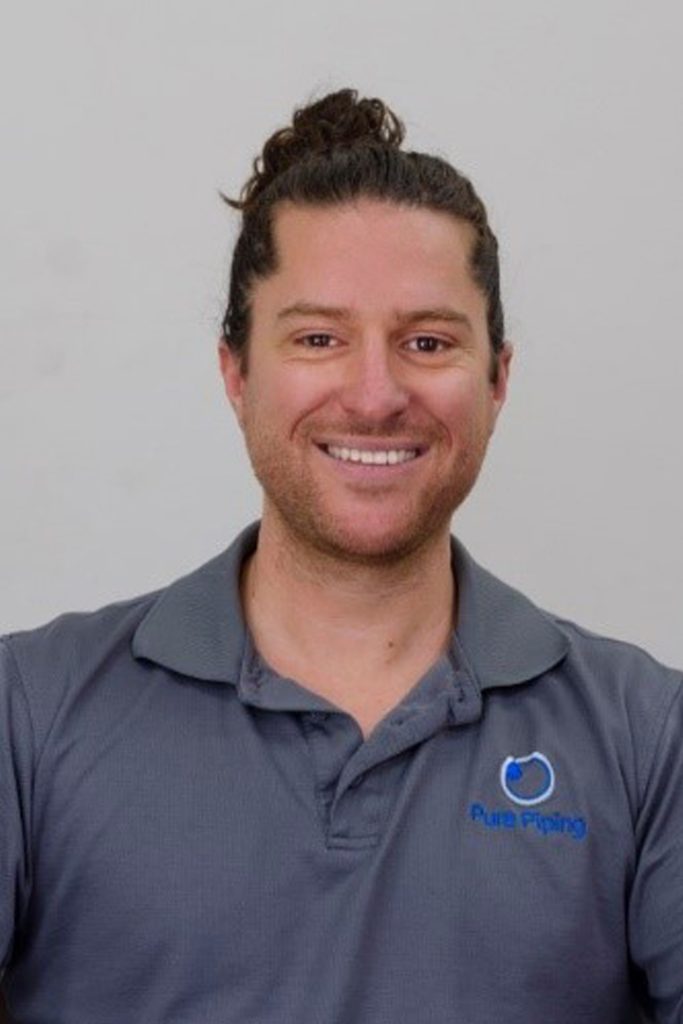
Chris Vella
General Manager
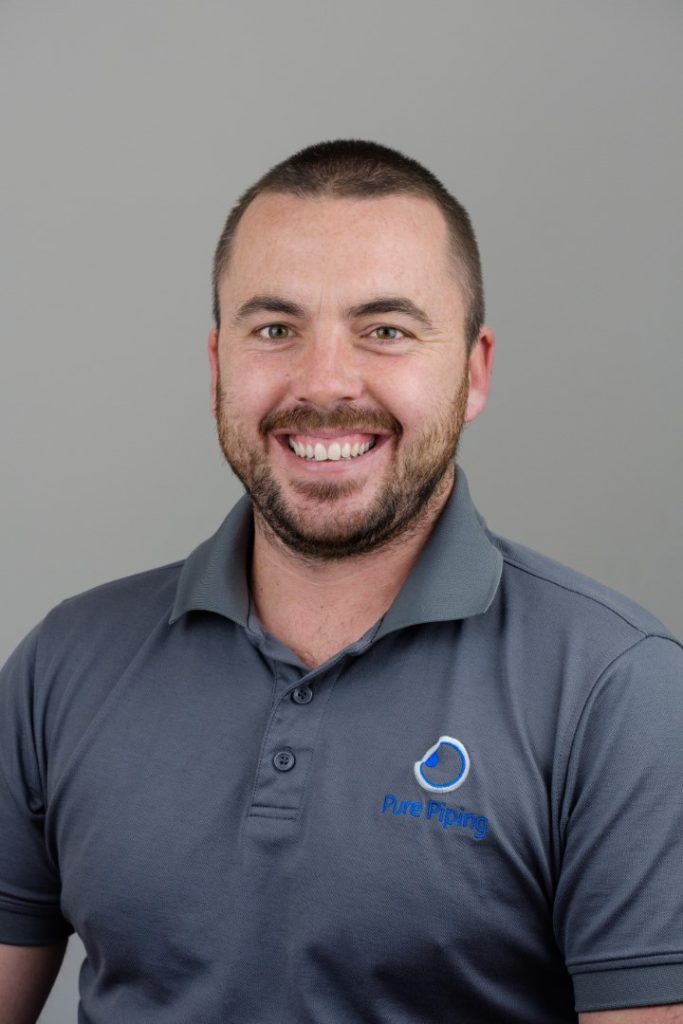
Ryan Warnock
Project Manager
